Demand for Li-ion batteries continues to grow in sectors such as electric vehicles, stationary energy storage, and consumer electronics. IDTechEx estimates that in 2023, total demand for Li-ion batteries was 750+ GWh across these sectors, which will increase to almost 10 TWh in 2043. However, potential constraints on the supply of critical raw materials (CRMs) for Li-ion batteries may be coming towards the end of the decade. This will see Li-ion battery recycling play an increasingly important role in the Li-ion industry.
Battery manufacturers and automotive OEMs will look to retain these CRMs within their supply chains to help meet the demand for new Li-ion batteries, while regulators will look to retain critical and strategic raw materials (SRMs) within their region’s borders to minimize dependence on supply from other countries.
EU Critical Raw Materials Act
On 13 November 2023, the European Union (EU) Parliament reached an agreement on the Critical Raw Materials Act (CRMA), but the Council must now formally approve these new regulations before publication in the Official Journal of the EU. This Act aims to retain CRMs within the EU and to “protect the Union from the rising gap between supply and demand at global level”. This will be important not only for the Li-ion battery market but also for other sectors, including security, defense, agriculture, health, and construction.
The document outlining these agreements, titled “Framework for ensuring a secure and sustainable supply of critical raw materials”, details 34 critical raw materials and 17 strategic raw materials. Critical raw materials are defined as those of high importance for the EU economy and subject to high levels of supply risk. Strategic raw materials are those of high economic performance, are used in technologies underpinned by green, digital, defense, or aerospace applications, and potentially subject to future supply risks. Materials most relevant to the Li-ion battery market that fall into both CRM and SRM lists include lithium, manganese, natural graphite, and nickel, alongside cobalt being listed as a CRM and copper being listed as an SRM.
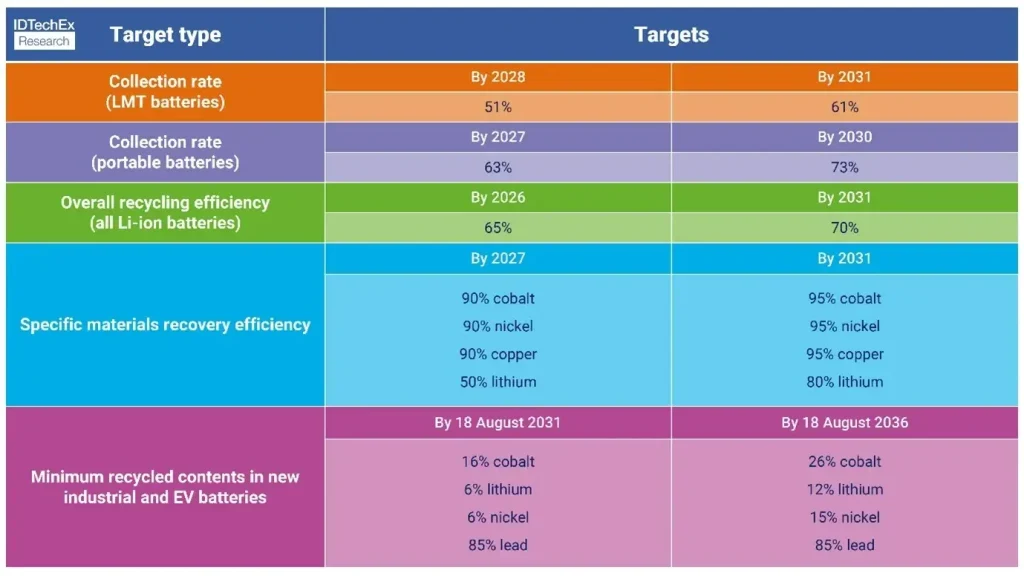
In order to retain these materials within the EU, the Parliament agreed on several objectives to be achieved by 2030 to reduce dependence on third countries. Firstly, no more than 65% of the EU’s supply of each SRM should come from a single third country in the hopes of reducing the EU’s dependence on China and diversifying its supply of SRMs. Secondly, at least 10% of the EU’s annual consumption of strategic raw materials should originate from EU extraction.
Thirdly, at least 40% of the EU’s annual consumption of strategic raw materials should be processed in the EU. Finally, and potentially most ambitiously, “Union recycling capacity should be able to produce at least +10% volume of recycling capacity based on the 2020-2022 baseline for each strategic raw material to at least collect, sort and process 45% of each strategic raw material contained in the Union’s waste taking into account technical and economic feasibility”.
The language in this statement may be unclear, as this does not explicitly stipulate if those batteries collected must be processed or recycled. For example, if a Li-ion battery were to be ‘fully’ recycled, this could be considered as the production of new cathode active material (CAM) from hydrometallurgical processing, which could then be used in new batteries. Whereas, if a Li-ion battery was to be ‘processed’, this could only involve the production of black mass via mechanical processing.
This black mass would require further refinement into battery-grade metal salts before further processing to produce CAM. This extra recycling step could arguably occur outside of the EU’s borders, but as long as 45% of the SRMs have been ‘processed’ in the EU, this statement could arguably be satisfied. Therefore, clearer and more explicit terminology is needed to ensure that these SRMs are retained within the EU at the final point of a given recycling process, which ensures the yield of usable materials in new batteries.
Comparison to EU Battery Regulation targets
It is important to consider how this compares to The EU Battery Regulation, which came into force in August 2023. These regulations detail the collection rate and recycling efficiency targets for Li-ion batteries.
By 2026, the recycling efficiency of Li-ion batteries should be at least 65% by 2026, and by 2031, this should be at least 70%; these targets are higher than the 45% recycling target in the CRMA. Collection rate targets for light means of transport (LMT) and portable batteries (which would contain several SRMs) in 2028 and 2027, respectively, are higher (51% and 63% respectively) than the 45% CRMA target by 2030.
Therefore, assuming the EU Battery Regulation targets are met, Li-ion battery recyclers will help contribute to the Union’s lower target of collecting, sorting, and processing 45% of each SRM. Regardless, this is still an ambitious target overall as these SRMs are used in wider sectors, too, thus creating a reliance on other industries whose products use these SRMs to meet these collection rates and recycling efficiencies.
Call for improved product design for improved circularity
The agreement from the Union also addresses that “recycling and re-use rates of most critical raw materials are low, including due to a lack of consideration of recyclability at the design phase of products”. Ultimately, this is holding back the potential circularity of these materials within supply chains, and thus, improvements to EV battery design, which allow for simpler and faster disassembly procedures, could be seen over the coming decade. This would help to improve the recyclability of EV Li-ion batteries.
As suggested in IDTechEx’s market report “Second-life Electric Vehicle Batteries 2023-2033“, improvements to EV battery design, such as the adoption of cell-to-pack designs, would remove the existence of a module and related connections, thus allowing recyclers and second-life repurposers to access cells for processing more quickly, safely, and economically (although cell-to-pack designs bring concerns with greater use of structural adhesives).
Historically, battery manufacturers and OEMs have focused on designing EV batteries to improve performance, safety, and lifetime. However, such statements from the Union may drive manufacturers to start designing their batteries with greater consideration for ease of end-of-life processing. Ultimately, benefits for designing, or penalties for not designing, new batteries with improved end-of-life processing capabilities may have to be introduced for such action to be realized.
Future critical and strategic raw materials outlook
The CRMA is vital for the EU to retain its critical and strategic raw materials within its borders and to reduce its dependence on the supply of these materials from third countries. Several targets by 2030 have been agreed upon, but the Council must formally approve these before being published in the Official Journal of the EU. The 2030 target to “at least collect, sort and process 45% of each SRM contained in the Union’s waste” is arguably ambitious.
While the EU Battery Regulation mandates higher targets for the collection and recycling efficiency of certain Li-ion batteries sooner than 2030, other industries that use SRMs will also need to ensure their collection schemes and recycling processes are able to help meet this target. At least in the Li-ion battery market, the push to retain critical materials within a region’s borders or supply chain is not only coming from a regulatory perspective, as manufacturers and OEMs also realize the importance of recycling, especially as demand is expected to continue growing rapidly over the coming decades.
Ultimately, every stakeholder in the value chain will play an important role in reaching these targets in the EU. For instance, it should be in the best interest of battery manufacturers and automotive OEMs to design their Li-ion batteries with improved circularity in mind, for example, through simplified designs that reduce the number of connections in an EV battery pack. This will improve the recycling efficiency while potentially reducing the costs related to manufacturers and OEMs re-obtaining their critical or strategic raw materials from Li-ion battery recyclers.